
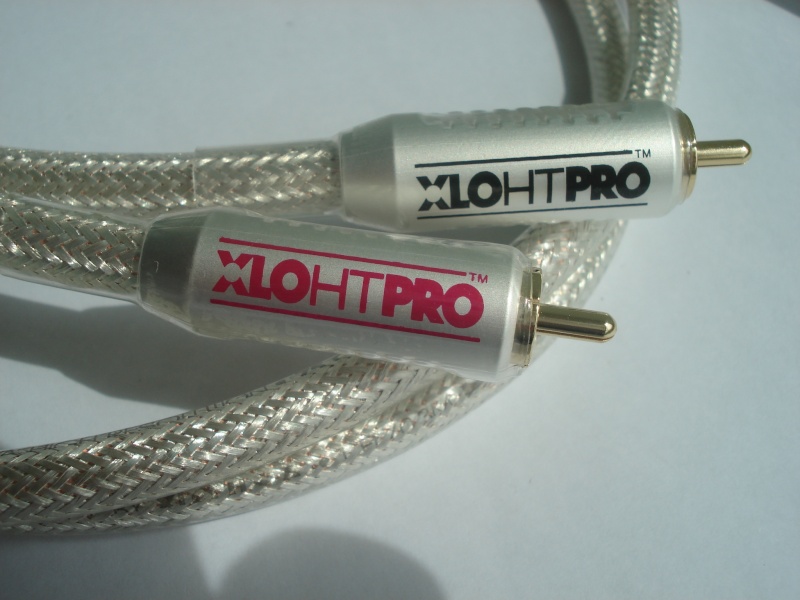
(11, 27) The printed inks containing MNPs are sintered typically at 120–200 ☌ depending on the metal, its sintering characteristics, organic ligands and the additives used in the ink formulation. (24-26) Although a palette of materials exist for printing conductive tracks, MNPs are still preferred for the manufacturing of circuitry due to lower complexity in the processing of inks containing MNPs and also better resolution and thermal stability compared to conductive polymers and liquid metals. In recent years, the use of inks containing MNPs, such as silver, (15-18) gold, (19) copper, (20) and other conductive materials including graphene, (21) carbon nanotubes, (22) poly(3.4-ethylenedioxythiophene) polystyrenesulfonate, (23) and direct writing of liquid metals such as gallium, indium and tin have been widely explored for printing circuits. Circuits that are traditionally printed in a single plane ( XY) using lithographic techniques can be designed to be printed in multiple planes using 3D printing, thus opening-up a whole new range of applications. Despite the advantages of the methods described above to fabricate MFAM components, embedding electrical components and printing conductive tracks, and injecting conductive inks into printed channels will limit the potential benefits that 3D printing has to offer.
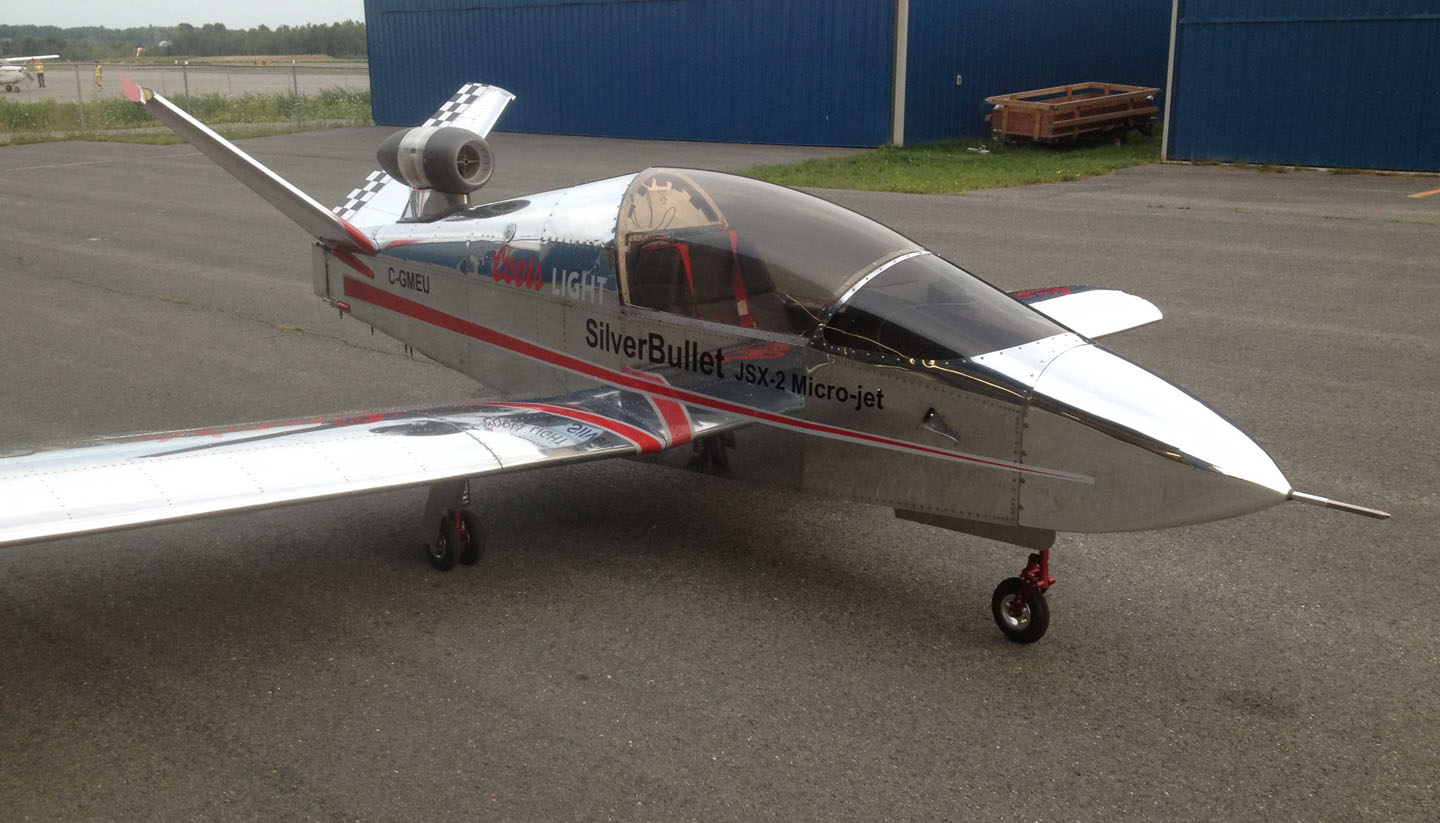
(9) fabricated dielectric structures using stereolithography and dispensed conductive inks to form electrical interconnects between components. (8) showcased 3D fabrication of sensors by integrating dielectrics with electronic components using a hybrid system. (1, 6) For example, Wu et al., (7) 3D printed parts with a hollow solenoid-shaped channel and injected silver inks to fill the channel to make them conductive for a sensing application. The studies that demonstrate fully 3D printed multifunctional structures (millimeters/centimeters in the Z direction) mostly involve fabrication of parts and components by using extrusion, stereolithography or jetting based printing techniques and embedding an electronic components into it. This study recommends the use of LS method to sinter the AgNPs to obtain a conductive track in 25% less time than SS method for MFAM.ĭespite the growing interest toward MFAM, the current fabrication of most printed electronics (such as RFID tags, (2) strain sensors, (3) humidity sensors, (4) and passive electronic components (5)) is limited to the nano/micron scale in the building ( Z) direction, that is, printing less than 20 layers. Electrical resistivity of the LS tracks (13.6 ± 1 μΩ cm) was lower than the SS tracks (22.5 ± 1 μΩ cm). The results depicted a homogeneous microstructure for LS of AgNPs and showed less deformation compared to the SS. Void percentage of both SS and LS samples was higher toward the top layer than the bottom layer due to relatively less IR exposure in the top than the bottom. The differences in the heat profile for the SS and LS was observed to influence the coalescence of the AgNPs. Multiple layers of silver were printed from an ink containing silver nanoparticles (AgNPs) and infrared sintered using a swathe-by-swathe (SS) and layer-by-layer sintering (LS) regime. This was achieved using a bespoke three-dimensional (3D) inkjet-printing machine, JETx, capable of printing a range of materials and utilizing different post processing procedures to print multilayered 3D structures in a single manufacturing step. With the view of enabling multifunctional AM (MFAM), in this study, sintering of metal nanoparticles was performed to obtain conductivity for continuous line inkjet printing of electronics. Despite the advancement of additive manufacturing (AM)/3-dimensional (3D) printing, single-step fabrication of multifunctional parts using AM is limited.
